Dish Network in Spartanburg has been an active and contributing member of the OpExChange for over fifteen years.
Through the years, they hosted numerous plant visits highlighting progression on their lean and operational excellence journey. They developed their own in-house lean six-sigma belt program and educated their entire workforce in lean manufacturing principles.
The culture at Dish embraced that operational excellence is a journey that does not have a final destination – it is a process of continuously improving the current state to bring value to the customer. Within the OpExChange, Dish became a model facility, frequently benchmarked for their continuous improvement culture and demonstration of improvements in both technology and employee development.
Dish Network is now on a new journey as they become the fourth major wireless provider in the United States, implementing the first open RAN 5G network in the nation. As part of this disruptive entry into the 5G market, the Spartanburg team put together a plan to transform their 317K square foot, set-top box remanufacturing facility. The plan included converting the site into an assembly and distribution operation for outfitting cellular towers, while simultaneously moving all their existing operations to a sister facility in El Paso, Texas.
The depth of the Spartanburg culture was truly tested during this transformation. This was a change for every single person at their facility. It required developing new processes and technology, changing jobs, learning new skills, and venturing into unknown territory. They successfully completed the transition in less than eighteen months.
In the OpExChange plant visit on June 9th, Sean Summey, General Manager for the Spartanburg site, and his tenured leadership team shared their experience with OpExChange peers. A sound foundation based on lean principles, employee engagement, and true trust relationships enabled them to be successful. The ninety-minute plant tour provided ample evidence that they are still an organization that is a model for visual manufacturing, operational excellence, and employee development.
Career Ladder – Opportunity
Sean stated that the number one benefit that Dish offers their team is opportunity. If an employee wants to learn and grow with the company, there are abundant possibilities, in Spartanburg and also across the United States. Dish developed a career ladder that visually displays not only paths within departments but also laterally into other groups. The levels are color-coded to indicate pay-scales. Separate departmental skill charts detail the individual certifications necessary to be eligible for each position. Employees may request training through an online portal.
Just because an employee has the required skills for a position does not necessarily mean they get the new pay grade. There is clear transparency on job opportunities. A job board on the production floor clearly displays the quantity of each position needed and the number of people currently certified to fill those positions.
During the plant tour, all the presenters were living examples of the career ladder growth at Dish. Sean asked each presenter to share what their first job was and how they progressed. Many of them started as entry level operators and developed not only in their departments but also within other functions and disciplines. When Dish hires employees, they do not focus heavily on experience, but look for three things: Energy, Intelligence, and the Need to Achieve. Sean explained that he is an example of the opportunity growth at Dish. When he started as a cosmetics supervisor in 2007, he did not know the first thing about manufacturing. He progressed through multiple departments and responsibilities and is now the General Manager of the plant.
Lean Culture Training
The Spartanburg facility has been on a lean journey since the plant opened in 2006. The leadership team realized that the heart of continuous improvement resides with workforce engagement. They developed their own in-house, lean six-sigma program. Approximately 27% of their workforce now has either a green or black belt. Propagation of this lean knowledge is one of the keys to their sustained lean culture. The folks graduating from the training go on to lead Kaizen or rapid improvement events (RIEs). Lean education is also included in their new hire orientation and is incorporated into the career ladder skill charts.
During one of the tour stops on the visit, Jon Kocak, supervisor of the cabinet assembly area shared several improvements the team made in safety and productivity that resulted from RIEs. Most of these originated from the employee suggestion “IDEAs” program.
Visual Workplace
One of the most impressive take-aways from the plant visit was the visual orderliness of the site. Visual cues for Kanban levels, material presentation, and assembly tools were clearly marked. A key lean tool that Dish continues to use is the 5S system where there is “a place for everything and everything is in its place.” Each department has a weekly 5S audit performed from a neighboring department. The audit board is visually displayed on a department communication board. A thirteen-week trend chart displays the historical 5S performance. Sean added that the 5S system and a visual workplace is important for many reasons – “It is important for quality. It is important for safety and for employee engagement.” He emphasized that coming to work in a clean, orderly workplace with a defined process reduces anxiety and helps the employee enjoy their time at the plant.
Leadership & Trust
Dish emphasized building trust relationships into their leadership program for about fifteen years now. Sean mentioned that the Speed of Trust®, a methodology from the best-selling book from Stephen M.R. Covey, was the basis for how they lead. He added that the huge change necessary in their operational direction required an entirely new level of trust. There were long hours involved with researching, mapping out new processes, and implementing new equipment. If they did not have a healthy foundation of trust, this transition could have gone much differently.
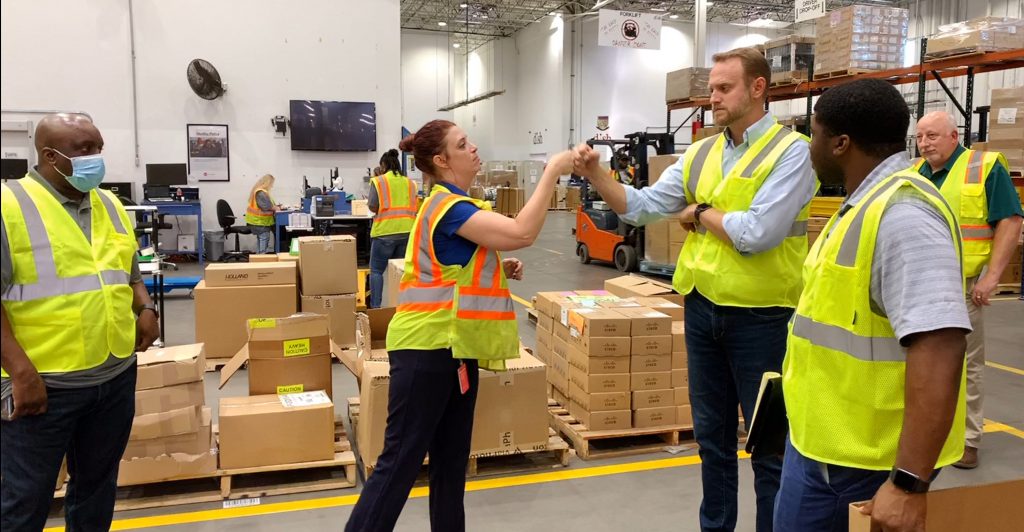
Sean Summey “fist bumps” Stacey Beasley after her kitting presentation. Stacey started as a 2nd shift tester 12 years ago and now supervises their Shipping/Expediting department.
Foundations for Improvement
When you walk through the assembly and distribution operation in Spartanburg, you would never guess that it was transformed in such a brief period. The team is engaged, the lean flow is orderly and apparent, and the team is focused on the next level of improvements. Employees greet you with a friendly smile and are eager to share their experiences with you. They answer questions honestly and even offer “lessons” learned from mistakes made along the way.
The Dish Network foundations of lean manufacturing principles, employee engagement, and trust relationships were the backdrop that made this transformation so hugely successful.
Sean encouraged OpExChange members to take advantage of the many plant visits and opportunities from their peers. “There is so much content in the OpExChange that we cannot consume it all. We’ve developed friends in this network that have helped us out during the years and particularly as we’ve stood-up this new shop.”
In the spirit of OpExChange collaboration, Dish shared documentation on their career ladder and 5S programs. These, along with full videos of the visit are available for OpExChange members on the OpExChange Portal.
About Dish Network
Dish Network Corporation is an American television provider and owner of the direct-broadcast satellite provider, Dish, and the over-the-top IPTV service, Sling TV. Dish recently acquired Boost Mobile and will be the fourth major wireless provider in the United States, implementing the first open RAN 5G network in the nation. Dish currently employees approximately 14,500 employees and provides services to nineteen million customers. Annual revenue for Dish is more than $17 billion.
About OpExChange
The OpExChange, sponsored by the South Carolina Manufacturing Extension Partnership, is a peer-to-peer network of companies in South Carolina known for generating success for members through benchmarking and best practices activities. Member companies host events and share practical examples of industrial automation, lean manufacturing improvements, and leadership development. It is an invaluable resource to South Carolina companies that provides access to others who are on similar improvement journeys. If you are interested in joining, contact Mike Demos (Mike@OpExChange.com) or visit the OpExChange website to see current companies: https://www.scmep-online.org/pages/memberlisting
Be the first to comment on "Dish Transforms Spartanburg Facility for 5G Buildout"