AO Smith, a company with a rich history dating back to 1874, has been at the forefront of manufacturing and innovation. From their humble beginnings producing baby carriages to their critical role in World War II, supplying bomb casings, nose gears for B-25 bombers, propellers, and landing gear, AO Smith has consistently pushed the boundaries of technology.
The company’s pioneering work in advanced welding techniques and glass-to-steel fusion revolutionized the manufacturing of products like pressure vessels, large-diameter pipes, and glass-lined water heaters. This innovation led to their prominence as a leading water heater manufacturer, introducing the first glass-lined water heater in 1936.
On October 22nd, OpExChange had the privilege of touring their impressive water heater plant in McBee, SC. The focus of this visit was to share the development of the AO Smith Operating System (AOSos).
The McBee Plant
The AO Smith plant in McBee spans nearly one million square feet. They began producing water heaters in October of 1980. They quickly ramped up production to produce one million water heaters in just over four years. This facility is currently the largest North American water heater plant and own approximately 51% of the total commercial heater market. They annually process about twelve million pounds of steel and 350 thousand pounds of copper. This site has been a member of OpExChange for nearly 16 years.
Refinement of the Manufacturing Operating System
Dan Royston is the Director of Operations at the McBee plant. He is a long-time employee of AO Smith with over 28 years with the company in a leadership role. He began leading the McBee site in 2018. During the visit, it was very apparent how proud Dan is of his team.
Drawing from his leadership experience, Dan knew that to truly connect with his new team, he needed to be present on the floor. During his first week, he made several daily rounds throughout the entire facility. On one of his initial walks, an outspoken operator known as “Hot Rod” approached him and said, “I need your help.” Seeing Dan’s willingness to listen, other operators soon followed suit, sharing their concerns and ideas. By the end of the week, Dan found himself carrying a notebook to keep track of all the feedback from his team.
Dan quickly identified an underlying issue in the plant—and it was not the workforce. He observed that employees were often left to tackle challenges on their own, lacking essential support from leadership. There simply were not enough leaders for the large workforce, and those who were present were constantly firefighting to keep up with customer demand.
The Toyota System – Leadership
In 2018, AO Smith’s senior leadership began having discussions with the Toyota Production System Support Center (TSSC), a non-profit organization affiliated with Toyota Motor North America. By late 2019, TSSC began collaborating with the McBee plant to revamp the AOSos.
Dan explained that instead of implementing the Toyota system across the entire plant all at once, they focused on a model line. Their strategy was to go “inch wide, mile deep,” allowing the team to learn through hands-on experience. This would allow them to have deep penetration of lean understanding and implementation. Once a particular area achieved sustained improvements, the approach could be scaled to other parts of the plant. They began with a bottleneck operation deemed critical to the plant’s overall success. To date, they have completed four model lines.
TSSC echoed the observation made by Dan regarding insufficient leadership. Toyota’s ideal ratio of team members to leaders is five to one. The McBee plant when they began this was a ratio of sixty to one. Dan and his team diligently worked on this. They actively filled many supervisor and lead positions, while training them in leadership and lean principles. Currently, the ratio of is much better at six-and-a-half to one.
The leadership team was taught the basics of the Toyota Production System (TPS) through workshops and visits from TSSC, focusing on the cores of a lean daily management system (LDMS) including leader standard work, visual controls, daily accountability, and leadership discipline. They also began deeper training in problem solving techniques with others in the model line.
Problem-Solving – A core of TPS
The Toyota System is rooted in problem-solving. Their belief is that problem-solving should occur at the lowest possible level within the organization. This means that employees directly responsible for the work should be involved in solving problems related to their area. They are also empowered to identify and address issues. In this “mile deep” approach, they trained their team to utilize the Toyota 8-Step problem solving process. This standardized process causes the problem solver to slow-down and break down the issues into manageable chunks. They utilize a standardized problem-solving flowchart to guide them and to capture their results. (Copy available on the Portal)
Dan shared that around one hundred employees have been trained in the problem-solving methodology. When asked about its impact, he enthusiastically responded, “This has drastically improved our operations. Now, instead of engineers directing solutions, our hourly employees are solving problems themselves – they know the job better than anyone.” He also highlighted that this approach has become a powerful tool for employee development, significantly boosting engagement. The employees take pride in their problem-solving results and are also gaining valuable skills, such as presenting their solutions. This enables them to go further in their career development at AO Smith.
The three operations folks participating in this activity were all promoted to higher leadership roles.
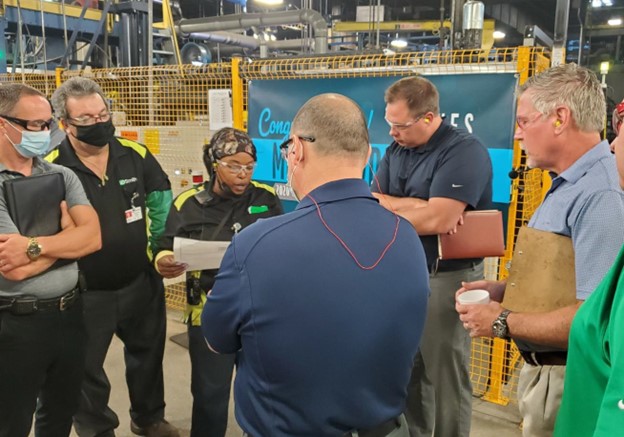
The three operations folks participating in this activity were all promoted to higher leadership roles.
During the plant tour, OpExChange visitors saw firsthand the results of the problem-solving efforts. In one example, Jaz, a team lead in Department 30, proudly presented a recent project. He guided the group through each of the eight problem-solving steps, explaining his decision-making process. With obvious pride, Jaz shared how his solution reduced rework and boosted cell output, all by creatively using existing materials in the process. “The best part,” he noted, “is that it didn’t cost us anything to implement!”
People Development & Standard Work
People are at the heart of the Toyota Production System (TPS), and a key focus of the AO Smith Operating System (AOSos) is developing team members at every level. This commitment begins with management, where each leader is expected to fulfill five essential roles:
- Show strong, visible commitment to AOSos.
- Develop a thorough understanding of AOSos principles and details.
- Make problems visible and foster a culture of problem-solving.
- Regularly engage with the front-line team.
- Commit to personal growth while developing others.
Dan emphasized that these roles are critical for sustaining AOSos. It is essential that the entire team sees leadership not only supporting AOSos but actively embodying and believing in it. Without genuine commitment, employees would see it as mere window dressing.
One of the tools AO Smith is rolling out is the work system map. This is essentially a standard work chart for a work area that incorporates the eleven ideal leader behaviors into the cadence of their work area. This is a visual tool in the area that identifies the workflow and main goal, items that support improvement and management, and the cadence of actions to drive ideal behaviors. It also incorporates a measurement called the Key Behavioral Indicator (KBI). (Copy available on the Portal).
This tool is being tested in their model line area. This includes monthly training for team leads, supervisors, and managers in utilizing the standard work tool.
The standardized work roll-out also includes the development of standardized work boards in all areas to drive visual management and improvement. Team leaders are trained in understanding takt time and cycle time. It also facilitates line balancing and resource leveling.
Lean Manufacturing: More Than Just a Methodology
AO Smith’s McBee plant serves as a powerful example of how Lean Manufacturing, when implemented with a strong philosophical foundation, can transform organizations. Lean is not merely a set of tools and techniques; it is a profound shift in mindset, emphasizing continuous improvement, waste elimination, and customer value.
At the heart of Lean is a deep respect for people. The McBee plant’s success hinges on engaging employees at all levels, empowering them to identify and solve problems. By fostering a culture of problem-solving and continuous improvement, AO Smith has created a workforce that is not only highly productive but also deeply invested in the company’s success.
Leadership plays a pivotal role in driving Lean initiatives. By actively participating in daily operations, providing coaching and support, and modeling desired behaviors, leaders can inspire their teams to embrace Lean principles. The McBee plant’s leadership team has demonstrated a strong commitment to Lean, leading to significant improvements in efficiency, quality, and employee morale.
About AO Smith
A. O. Smith Corporation is one of the world’s leading manufacturers of residential and commercial water heaters and boilers, offering a comprehensive product line featuring the best-known brands in North America, China, India, Vietnam and Europe.
The company was founded in 1874 in Milwaukee, Wisconsin, where today the Company is headquartered. A. O. Smith employs over 12,000 individuals at operations in the United States, Canada, Mexico, China, India, the United Kingdom and the Netherlands. We also have sales and distribution in more than 80 countries around the world.
As a global leader, A. O. Smith and its employees pride themselves on applying innovative technology and energy-efficient solutions to products marketed worldwide. The Company’s goal is to be a leading global water technology company, and our focus is on building this platform through new product development, global expansion, strategic acquisitions and partnerships. https://www.aosmith.com/
About OpExChange
The OpExChange, an SCMEP program, is a peer-to-peer network of manufacturers and distributors in South Carolina known for generating success for members through benchmarking and best practice sharing. Member companies host events and share practical examples of industrial automation, lean manufacturing improvements, and leadership development. It is an invaluable resource to South Carolina companies that provides access to others who are on similar improvement journeys. If your company is interested in participating in this collaborative effort to improve both the competitiveness of your operation and South Carolina, contact Mike Demos (mdemos@scmep.org). More information and upcoming plant visits are available on the OpExChange website www.OpExChange.com.
Be the first to comment on "Lean Manufacturing & Leadership: A Winning Formula at AO Smith McBee"